Addressing the automotive skills shortage
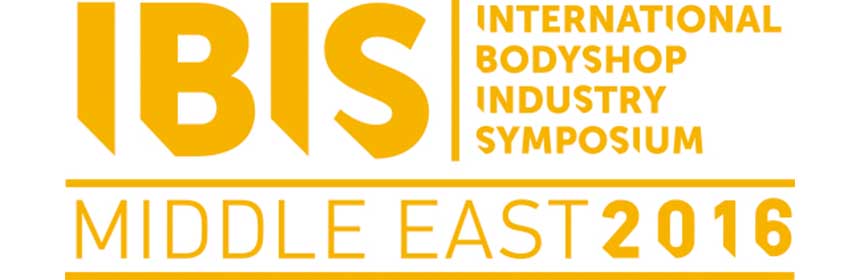
- February 11, 2016
- Posted by: Alan Feldberg
- Category: IBIS News
We’ve all been there – by the time we’ve got to grips with one technology five more have emerged. This is especially true in the automotive industry, which is going through arguably its greatest technological revolution.
These days no one person can be expected to cover all bases – the skills required to repair a car have more than doubled since the 1970s and that escalation is only going to accelerate. So building a workforce and creating a working environment that embraces learning, development and diversification is one of the key challenges in the industry today.
It sounds obvious, but getting and then keeping the top talent is a foundation stone for any successful business. In the Middle East, this challenge is particularly acute where labour migration has kept the industry afloat for years.
Recruitment
Traditional recruiting methods might not be fit for purpose in this industry and region. Sourcing potential employees through an agency, pre-screening them with a series of tests and then conducting face-to-face interviews, often at considerable cost, is an expensive and time-consuming process – and it’s no guarantee of success.
The first thing employers need to decide on is what they’re looking for. With so many new and varied skills required, they need to pinpoint exactly what they need for their business.
But even candidates who tick all the boxes might not be suitable. Meeting the technical requirements is just one element and employers bringing new employees to the Middle East need to make sure they’re prepared culturally and environmentally.
Lawrie Martin, director of operations, TTi Global, who spoke about the skills crisis at IBIS Middle East in Dubai at the start of February, said, ‘Businesses need to make sure new employees are work ready. That goes beyond technical skills and includes things like communication, team work, problem solving, initiative, planning and organisation, self-management and learning.’
He suggests a more innovative approach to recruitment that leans heavily on online assessments. Apart from enabling businesses to seek out the specific skills they’re after, and then testing them, Lawrie believes this less intimidating approach gives employees the best chance of success. He also suggests introducing post-test assessments to enable the candidate to brush up on areas they’re lacking and then try again.
He said, ‘Compared to flying everywhere, it’s also low-cost. But you need to be specific in your skill requirements.’
Retention
A recurring issue in the Middle East is employees using their first job in the region as a gateway to other jobs. So getting the right person is only half the battle; retaining them requires a multi-pronged approach that goes beyond salary.
Recognition and personal development both go a long way to making a happy employee. One good tip Lawrie suggests is including the family – if an employee does well, let their family know. Four positive comments to every one negative is a useful ratio to work from.
When it comes to training, it can be an expensive business for bodyshops in the region as often it’s OEM-driven. Lawrie suggests broadening the net to search globally for training providers, and says that the solutions to real-world problems can often be found in virtual reality solutions. After the initial software outlay, simulated painting or welding doesn’t carry any equipment expenses, while m-learning and gamification learning apps can also be economical and effective.
Lawrie said, ‘We need to ask if our traditional training models will work in the future, and if not we need to adapt new styles of learning. There might be an initial outlay, but it’s cost-effective in the long-run.’
But, says Lawrie, the skills shortage within the automotive industry will only intensify if the image it portrays to the outside doesn’t change.
He said, ‘The perception of the industry worldwide is that it’s a dirty trade. But there is amazing stuff in our industry, space-age technology and innovation. There’s no silver bullet. There will still be parents who want their children to be a doctor or an engineer, but the only way we can improve our industry is by improving the organisational behaviour and the perception of the manpower within it.’
BOX OUT
The skills challenge:
- Do we have the people to meet new technological challenges?
- Are we retaining them?
- Will our traditional training model work in the future?
- Are we do enough training?